Telkwa’s Deep Collaboration on a Mini Biomass District Heating System
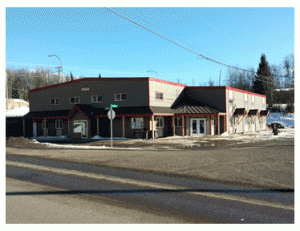
The Village of Telkwa turns the need for a new municipal office into an innovative community partnership on a biomass district energy system at Hankin Corner.
Project Summary
The Village of Telkwa took climate action in the building sector by retrofitting an existing derelict building for a new municipal office and installing a biomass boiler district heating system (the system).The system generates heat energy, through burning wood, which is then transferred into a distributed hot water heating system to heat their municipal office and neighbouring buildings.
The project was part of the implementation of the Village Official Community Plan (OCP) and Integrated Community Sustainability Plan (ICSP). The Village plans prioritize repurposing old or abandoned buildings before building new ones. The plans also call for climate change mitigation measures. Based on these plans the Village acquired an abandoned building in 2011 when the old Village Office became unfit for occupation.
The abandoned building was close to an elementary school, a restaurant, a vacant bakery and five single residential homes – all buildings that could benefit from a biomass district heating system. They became partners. With the partnership between the school, residences and commercial sector the district heating system became a feasible option as a clean alternative energy solution to heat a portion of the downtown core.
Construction began in early fall of 2013. The biomass to fuel the boiler was sourced from wood chips produced locally from reject wood slabs supplied by a local sawmill and from standing deadwood.The 300 kilowatt (KW) biomass boiler was officially running by November 2013. The municipality started distributing heat to the school immediately. Businesses and residences were brought on incrementally. The building was big enough to include approximately 5000 square feet of rental space. New businesses are being added to the partnership and connected to the system as spaces are leased.
The municipal system is now the primary supplier of heat for the partners. The heated water generated in the new system supplies the partner buildings through their retrofitted existing electric and natural gas infrastructure.
Original systems are available for backup. For example, the gas boilers in the Telkwa Elementary School act as a backup system to the Village biomass system. While the biomass system is the primary energy source – backup is needed if the temperatures approach -30C or cannot otherwise keep up with the cold weather demands required by the entire district heating system.
Not only does the Village now run an innovative district energy system and have municipal offices that use less energy, they have improved the overall community design with a great looking building.
The project was managed internally by the Village’s Engineering Department. Telkwa’s past Director of Engineering was the lead project manager. Telkwa’s Engineer Technologist Scott Beck assisted with project management and oversaw the renovation to the building. “It’s been a positive influence on the community” says Beck, “the newly completed property has spearheaded community involvement – we are seeing other businesses improving their properties as well.”
Energy Savings/GHG reductions
The district heating system can replace 90% or more of required heating energy and save the consumer up to 35% in heating costs.
Heat energy generated by biomass boilers is different and cleaner than heat energy generated from conventional wood burning stoves. The biomass boiler system is designed to control and reduce emissions. As a result, carbon dioxide (CO2) reduction is estimated to be over 110 tonnes a year while having capacity to generate 300 Kilowatts (kW) energy per hour.
“It’s been a positive influence on the community and spearheaded community involvement.” – Scott Beck
Business case
The Village office is closely tracking the cost versus pay back of the system. The system is relatively new (at the time of publishing this case study), therefore calculations on return on investment are just starting to emerge.Projections estimate a mildly positive return on investment in coming years with a current expectation to be revenue neutral, with heat savings going to property and building owners.
The feasibility study prior to the project cost $25,000. The total actual project cost was $704,320.00, the installation of the district heating system portion of the project cost was estimated at $396,980. A complete exterior retrofit was estimated at $247,250. The remaining $60,090 was spent on building retrofit improvements and boiler fuel storage.
Financial support for the feasibility study ($25,000) came from the Omenica Beetle Action Committee and expertise from the Wood Waste to Rural Heat Initiative. The Federal Gas Tax Innovation Fund provided $644,230.00. The remaining expenses totalling $60,090 came out of the Village budget. Northern Development Initiative Trust later provided an additional grant to build three commercial rental spaces.
The Village and School District will save money on future carbon taxes because of the reduction of natural gas used to heat the municipal office and Telkwa Elementary School.
Staff at the Village of Telkwa estimate that the annual carbon tax savings would be approximately $2,850. This comes from an estimated savings in energy of 1740 GJ converted to greenhouse gas emissions (114 tonnes) and multiplying by the carbon tax ($25 per tonne of GHG emissions).
In addition, the municipality charges for heat supplied to partners. The municipality is not a British Columbia Utilities Commission (BCUC) regulated utility company; it supplies heat to the buildings that are connected to the system through energy service agreements. Building energy meters are used to measure consumption. The data is recorded and then used to invoice property owners; at a reduced rate – about 20-25% less than the current rate for natural gas.
The consumer benefits from an approximate 35% reduction in heating costs due to a combination of factors; delivered efficiencies, existing equipment efficiencies, building envelope efficiencies, and distributed heat through hydronics versus forced air.The system’s wet heat (water) is more efficient than forced air. The system is more efficient than existing electric or natural gas systems which typically have a higher heat conversion loss. Any losses in existing systems are negated by being connected to the new system resulting in cost savings.
The system was built to accommodate future expansion at minimal cost. The Village receives rental income from leased retail space with potential for more rental income as more businesses are brought on board.
Co-Benefits
The biomass system is now a focus for community education and engagement around energy options. The commercial space for local businesses is also now a driver of economic development. The improved aesthetics of the community makes the Village more appealing for tourism, business development and attracting new residents as well as creating a public meeting space for the community.
Lessons learned
Start early with a collaborative, multi-disciplinary approach
Telkwa urges other local governments considering constructing a biomass district energy system to research the long-term reliability and cost of the wood chip supply and ensure the chips are compatible with the boiler system installed. There can be challenges to getting the chips and pellets at an economical cost.
The Village is proud of its ability to act as the General Contractor. By doing so, the Village was able to reduce costs and make changes and/or decisions quickly when required. Furthermore, once the boiler was installed the Village was able to quickly hire local contractors to complete the remaining building retrofits and connect the system to the other properties.
Local government contact
Scott Beck
Engineering Technologist, The Village of Telkwa
P: 250.846.5212
E: scottbeck@telkwa.com